
Screw Press
Huber Screw Press – The Most Efficient Sludge Dewatering System
The Huber Screw Press is a highly efficient, low-energy solution for sludge dewatering for primary and secondary industrial sludge. Designed for continuous and automated operation, it delivers maximum dry solids content with minimal operator intervention.
With over 1500 units installed worldwide, it features advanced German engineering, utilising a slow-rotating auger and precision-built screening drum to ensure high capture rates while preventing clogging. Its compact, stainless steel construction offers durability, easy maintenance, and long-term reliability.
Several HUBER Q-PRESS® models are available with capacities ranging from 90 to 540 Kg Dry Solids (DS) per hour to suit virtually all industrial applications for dewatering of primary or secondary sludge.
Some of the key features of the HUBER Q-PRESS include:
- High performance equivalent to and often better than centrifuges and belt presses
- Very slow speed screw, which prolongs life, with minimal service required
- Very low energy requirement compared to centrifuges
- Very low wash water requirements
- All stainless steel construction and high-quality fabrication in Germany
Principle of Operation
The machine consists of a main case, internal screw rotating at <1.5rpm, spray bar and cylindrical wedgewire/mesh drum. As the sludge enters the unit the sludge is conveyed by the screw through the drum length whilst the filtrate is drained through the mesh. The drum consists of variable apertures and profiles, and together with a reduced screw pitch and increased shaft diameter, pressure is gradually applied to the sludge mass as it travels up the drum.
An adjustable pneumatic cone is configured to set the pressure at the outlet to optimise the operation of the unit and achieve maximum sludge dryness.
The cake is discharged through the cone into a bin or conveyor system, and the filtrate that collects within the main case is discharged via gravity to the filtrate outlet flange.
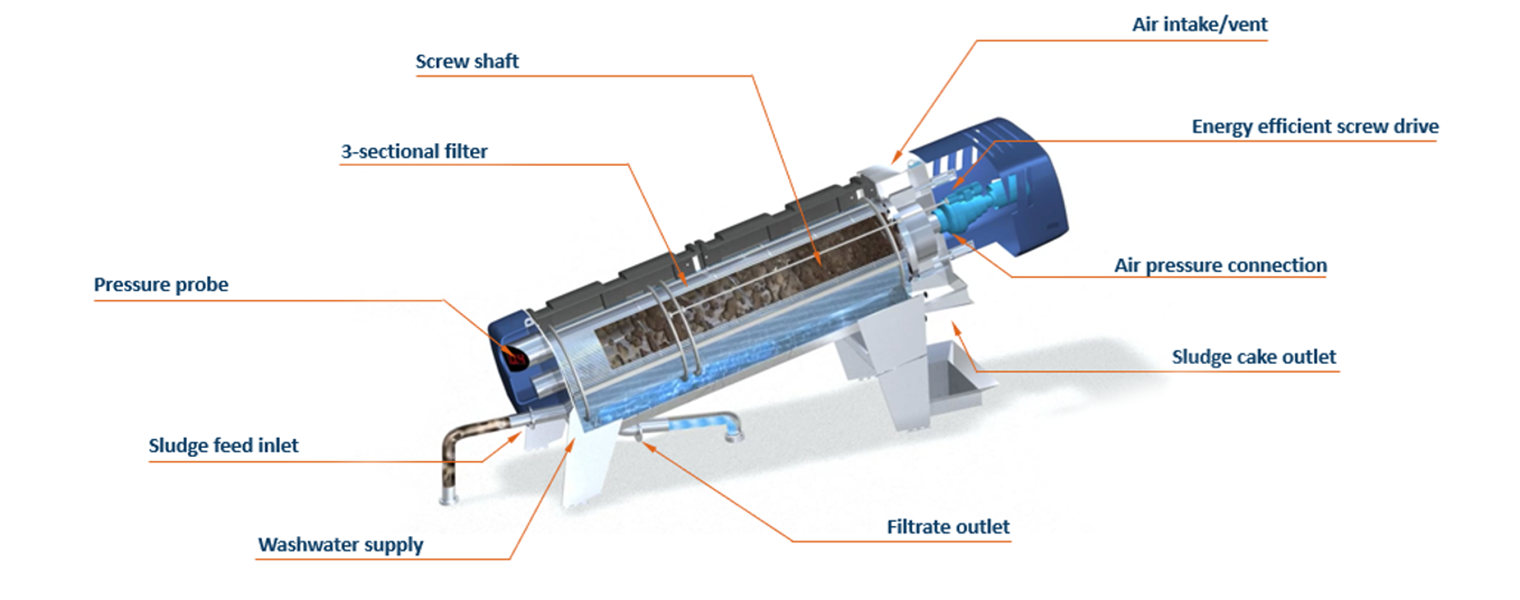
Capacities
There are currently 4 models in the Huber screw press ranging in capacity to process a dry solids load from 90 kg/hr to 540 kg/hr.
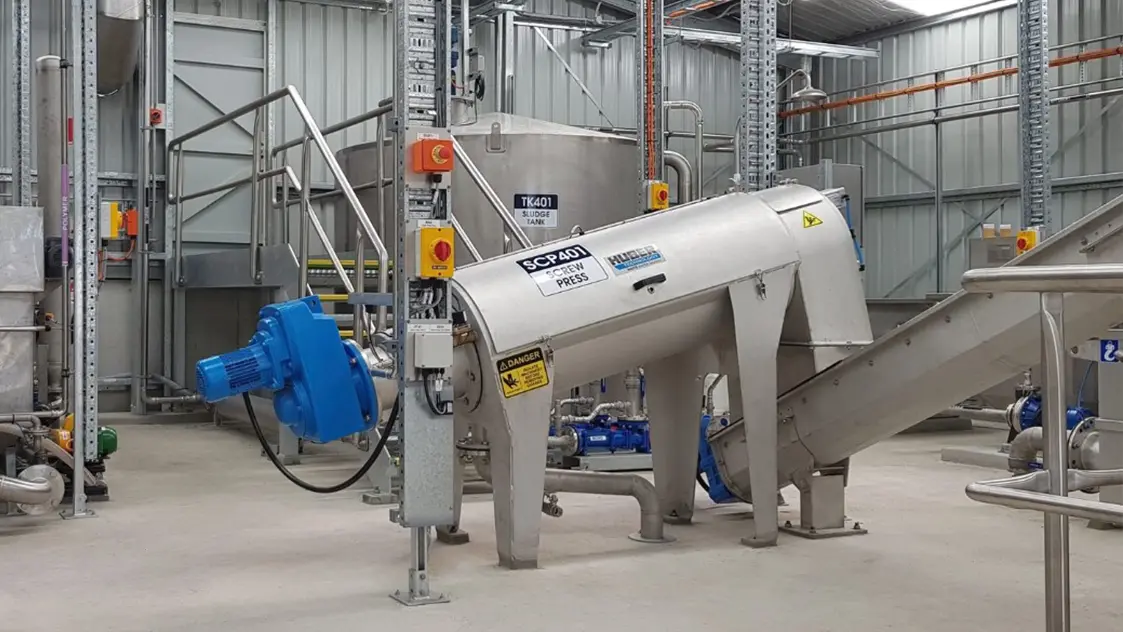

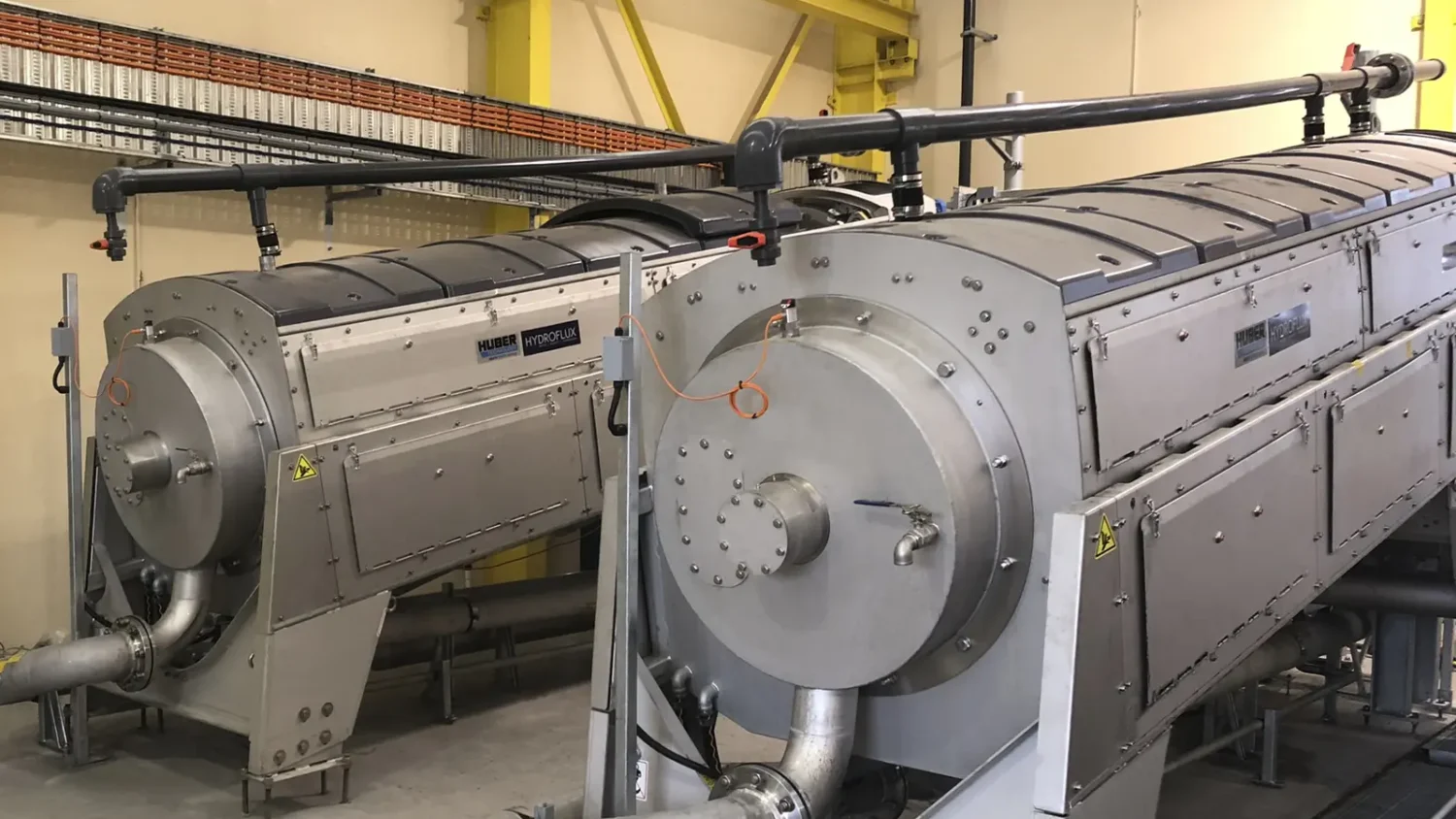
The table below shows the nominal design capacities of the models available.
Model Number | Max Hydraulic Flow (m3/h) | Max Solids Load (kg/h) |
RoS3Q280 | 2 | 90 |
RoS3Q440.2 | 4 | 180 |
RoS3Q620.2 | 10 | 350 |
RoS3Q800.2 | 20 | 540 |
Configurations
There are many ways in which a screw press dewatering plant can be configured, depending primarily on logistics and the method of dewatered solids removal. Factors such as plant layout, available space, sludge volume, and disposal requirements influence the design. Dewatered solids can be discharged directly into bins, hoppers, or conveyors, which may then transfer the material to trucks, skips, or storage silos for further handling.
In some cases, enclosed conveyors or screw augers are used to transport sludge to designated disposal or reuse areas, ensuring efficient, clean, and automated solids management.
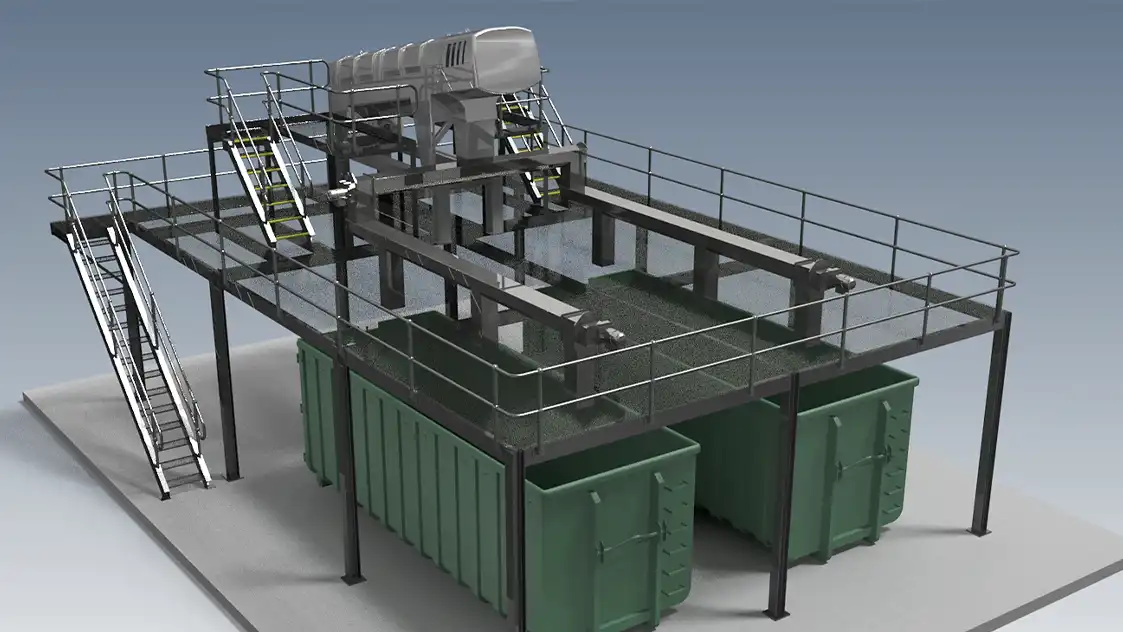

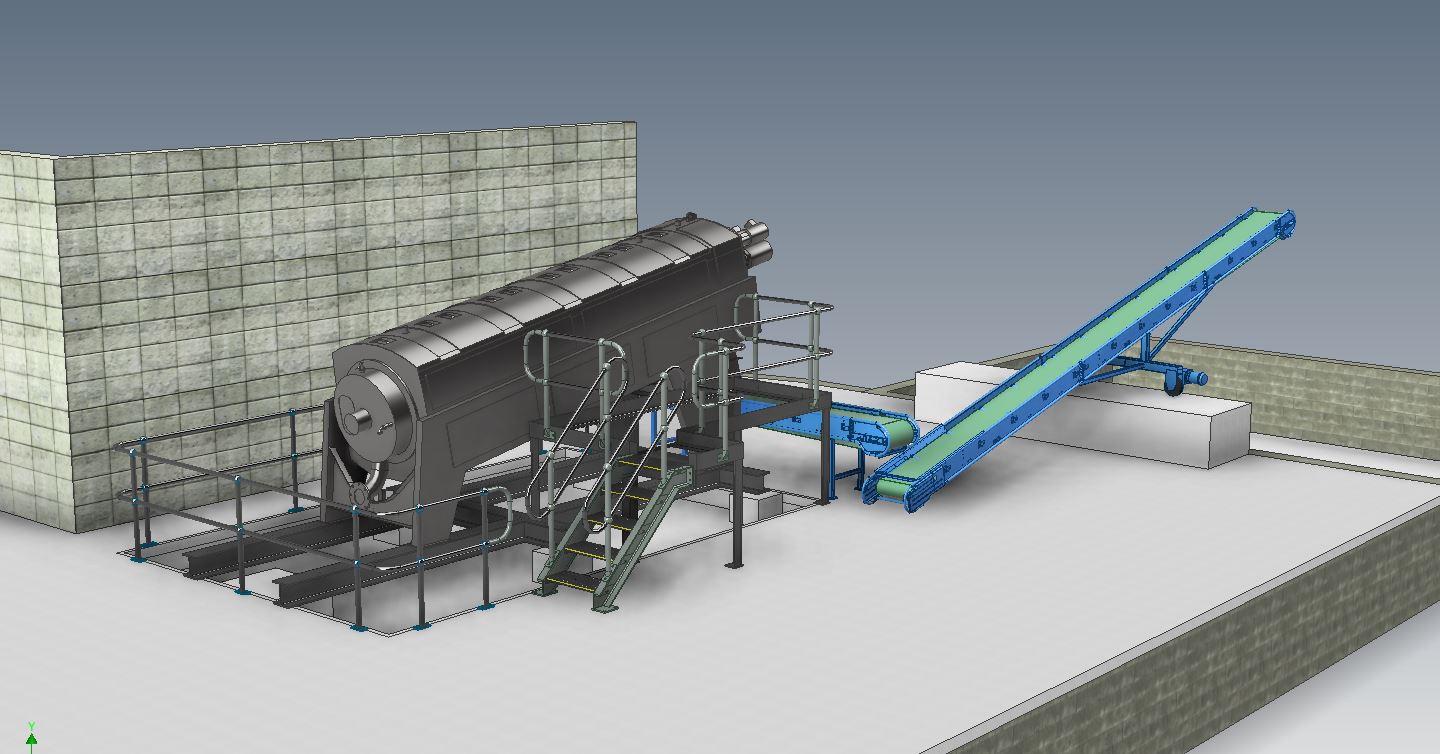
The configuration is tailored to optimise operational efficiency, site constraints, and handling requirements, providing a streamlined and cost-effective sludge management solution. Please get in touch to discuss sizing and configuration options for your site.
Maintenance
The HUBER screw press is designed to require minimal maintenance and typically only once every few years access to the internal screw is required. The latest range of larger machines offers a spilt basket to simplify access to the internal components without the need to remove the main screw.
The following diagrams show the top half of the basket being removed for screw wiper replacement in situ, a task that is only required every few years.
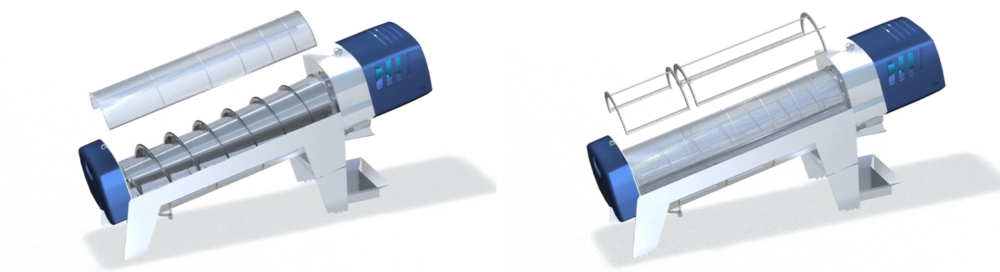
Regular maintenance primarily consists of basic cleaning, routine oil changes, and lubrication, all of which can be easily performed by in-house personnel without the need for specialised technicians. The design of the Huber Screw Press ensures that maintenance access points are easily reachable, simplifying servicing tasks. For plants looking to further streamline maintenance, optional automated lubrication systems and condition monitoring sensors can be integrated to provide real-time performance data and early detection of potential issues.
Screw Press FAQs
For sludge generated from primary treatment processes, such as Dissolved Air Flotation (DAF) and clarification, the Huber Screw Press is an ideal solution and can achieve 35-50% dry solids (DS). The dry solids content is primarily determined by the sludge composition itself, rather than the efficiency of the machine, as the screw press removes all free water under maximum compaction. The DS content is also influenced by any chemical treatments applied during the primary treatment process and to the sludge.
For waste activated sludge (WAS), which is produced in secondary biological treatment plants, the screw press typically achieves 12-15% DS, which is the maximum attainable for WAS.
Hydroflux has successfully installed many screw presses that dewater a combination of primary and secondary sludge, with resulting DS values falling between the above ranges, depending on the relative volumes of primary and secondary sludge being treated.
The amount of polymer required for dewatering sludge with a Huber Screw Press depends on several factors, including the type of sludge, its composition, and the desired level of dewatering. For primary sludge generated from Dissolved Air Flotation (DAF) or clarification processes, polymer dosages typically range from 1 to 5 kg of polymer per ton of dry solids (kg/t DS). This dosage is heavily influenced by the polymer dosage already applied in the primary treatment plant.
It’s essential to optimise polymer dosage through trial and error to identify the most suitable type and amount of polymer for each specific application. The effectiveness of the dewatering process can be compromised by using either too much or too little polymer. Regular monitoring and adjustments of the polymer dosage are often necessary to achieve the best possible dry solids content while minimising chemical costs. This process can be simplified if there are adequate storage facilities to ensure the sludge is well homogenised, maintaining consistency and minimising the need for constant adjustments.
Huber Screw Press Animation
This video highlights the Huber Screw Press’ simplicity of operation and low maintenance requirements. It demonstrates the continuous dewatering process, featuring the slow-rotating screw mechanism that minimises wear and reduces energy consumption.
The animation also illustrates the highly efficient cleaning system, which utilises automated washing and wipers to maintain optimal performance. Towards the end, the video explains the straightforward maintenance procedures, which are typically required only once every few years.
These features make the Huber Screw Press a cost-effective, reliable, and hassle-free solution for sludge management, making it the dewatering system of choice for many industries.
Why choose to work with Hydroflux Industrial?
Hydroflux’s team includes qualified civil, mechanical, chemical, and electrical engineers, as well as experienced project managers, site supervisors, commissioning engineers, and service technicians. With offices located across Australia, Hydroflux ensures a strong local presence throughout the duration of every project. All projects are carried out under externally certified occupational health and safety and environmental management systems.
Hydroflux designs and constructs comprehensive wastewater treatment systems that incorporate various types of processing equipment, including screens, physical/chemical, biological, and tertiary treatment technologies to enable high quality discharge or water reuse. Below is a 3D drawing of a treatment plant constructed by Hydroflux that incorporated balancing, heat recovery, rotary screening, DAF, and sludge dewatering. Contact us for a technical discussion about how we can assist you with your wastewater treatment facility.
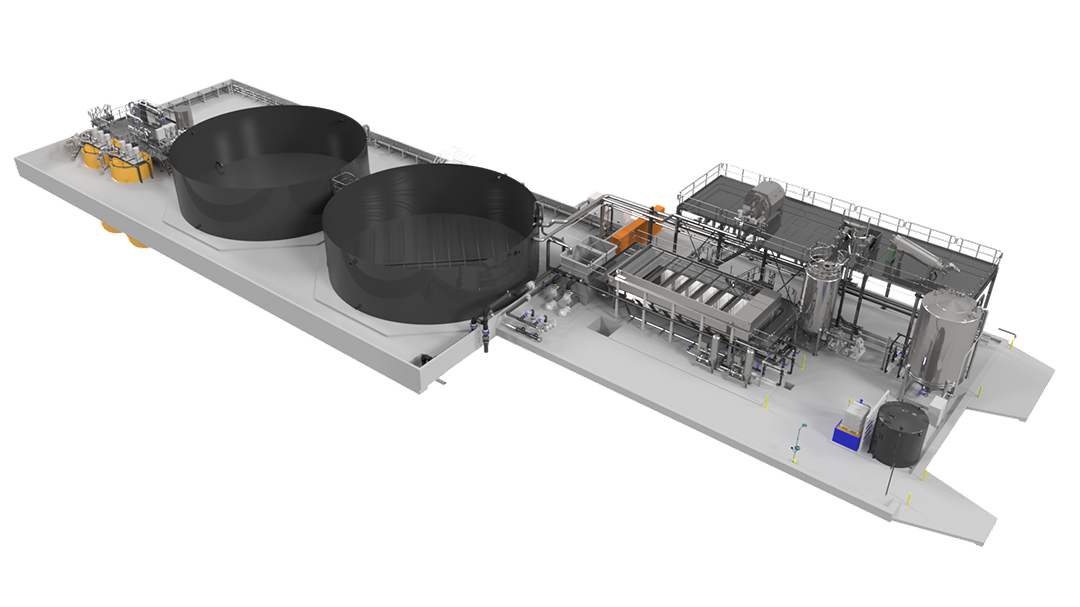
Sustainable Solutions
As Australia’s first certified carbon-neutral water and wastewater chemical supply and service business, we focus on sustainability. Developing and delivering sustainable solutions for treatment plant operation and maintenance is at the core of what we do. Our equipment is the most sustainable in the Australian and New Zealand markets and is also carbon-neutral. Click here to find out what this means for you.
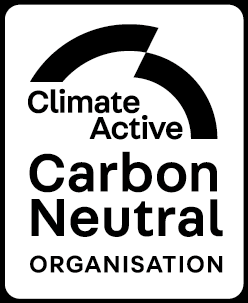