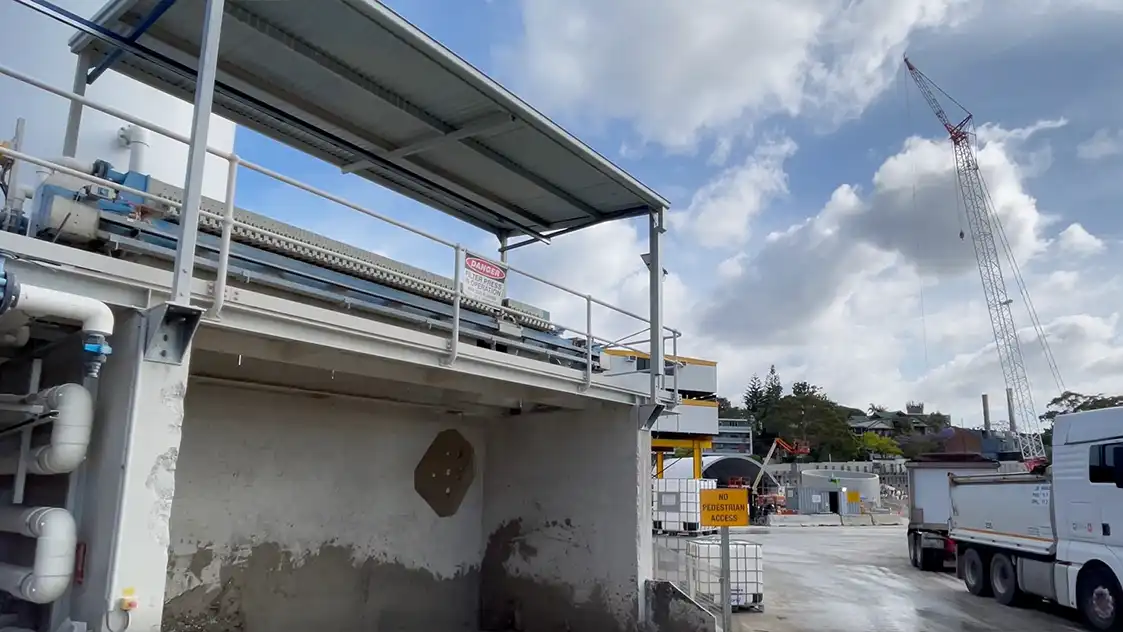
Filter Press
Hydroflux CakeMax® Filter Press – Advanced Chamber Filter Press Dewatering
The Hydroflux CakeMax Filter Press is a reliable and efficient dewatering system designed to maximise dry solids content while minimising sludge volume. Engineered for performance and durability, the CakeMax Filter Press produces a high-solids filter cake, reducing disposal costs and improving operational efficiency.
Suitable for many industrial applications, including mining, manufacturing and infrastructure projects, the Hydroflux Filter Press is available in various sizes and configurations to meet specific process requirements. With options for semi-automated and fully automated operation, it ensures consistent, high-quality dewatering results.
Key Advantages of the CakeMax Filter Press include:
- Produces an exceptionally dry filter cake, often outperforming other dewatering technologies
- Requires minimal operation, with options for automated plate shifting or extended cycle times
- Low water consumption, with little to no wash water required
- Highly cost-effective, offering a low capital investment
- Minimal or no chemical usage, reducing operational costs
- Simple maintenance, easily managed by an in-house maintenance team
- Fast and straightforward startup and shutdown processes
How the CakeMax Filter Press Operates
The CakeMax filter press consists of a series of interconnected plates with filter cloths held together by a hydraulic ram. These plates create voids between them, where dewatering occurs as the feed pump applies pressure to the slurry. The process typically starts with chemical conditioning, where polymer is added to the sludge to bind particles into larger flocs, improving dewatering efficiency, however, in some cases, dewatering can be achieved without the use of chemicals.
Dewatering Stages
- Preparation – The chamber is sealed closed by a hydraulic ram, ready for sludge intake.
- Filling – Wet solids are fed into the chamber, gradually filling the voids.
- Filtration – As pressure builds, water is filtered through the filter cloths and drained away.
- Completion – When the set pressure is reached, the feed stops, marking the end of the dewatering cycle.
- Cake Release – The hydraulic ram retracts, and the plates open manually or automatically, allowing the dried sludge cake to drop into a bin or conveyor for disposal.
This efficient, high-performance system ensures optimal sludge dewatering with minimal operator intervention.
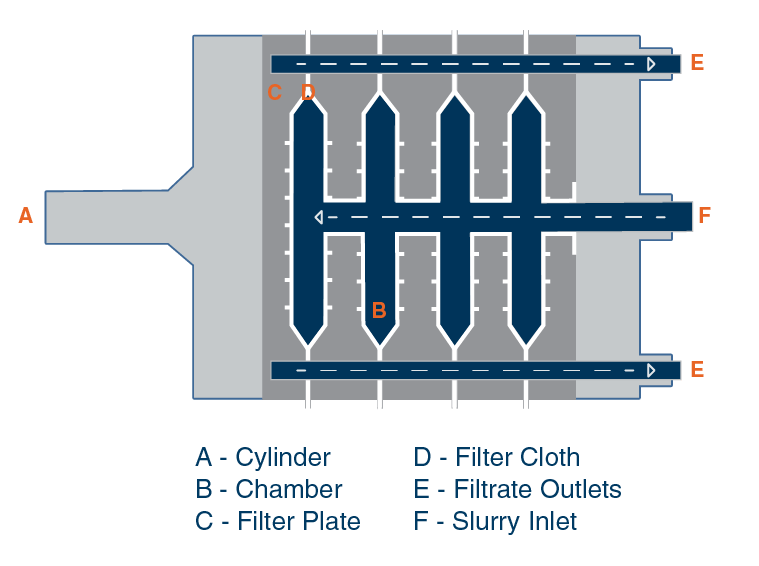
Automation
CakeMax Filter presses can be semi-automatic or fully automated. Semi-automatic CakeMax filter presses rely on an operator to release the hydraulic ram once the dewatering cycle is complete. Once the pressure is released, each of the plates are pulled apart, allowing the filter cake to drop into a bin below.
The fully automated CakeMax filter press uses a pneumatic plate shifter to open the plates automatically once the press has completed the dewatering cycle. Automation of the CakeMax filter press considerably increases the daily capacity of the unit by increasing the number of cycles that can be completed without operator intervention.
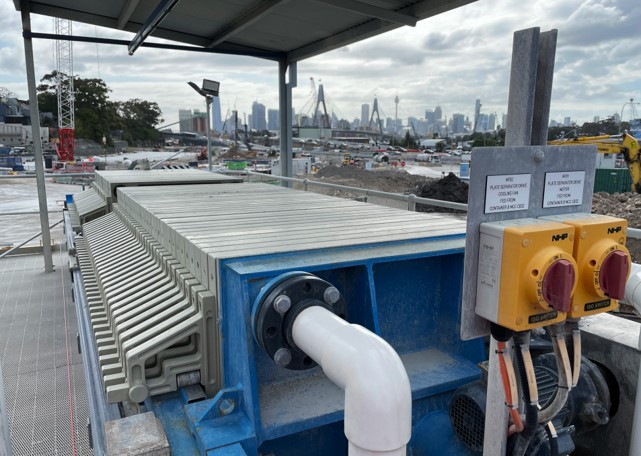
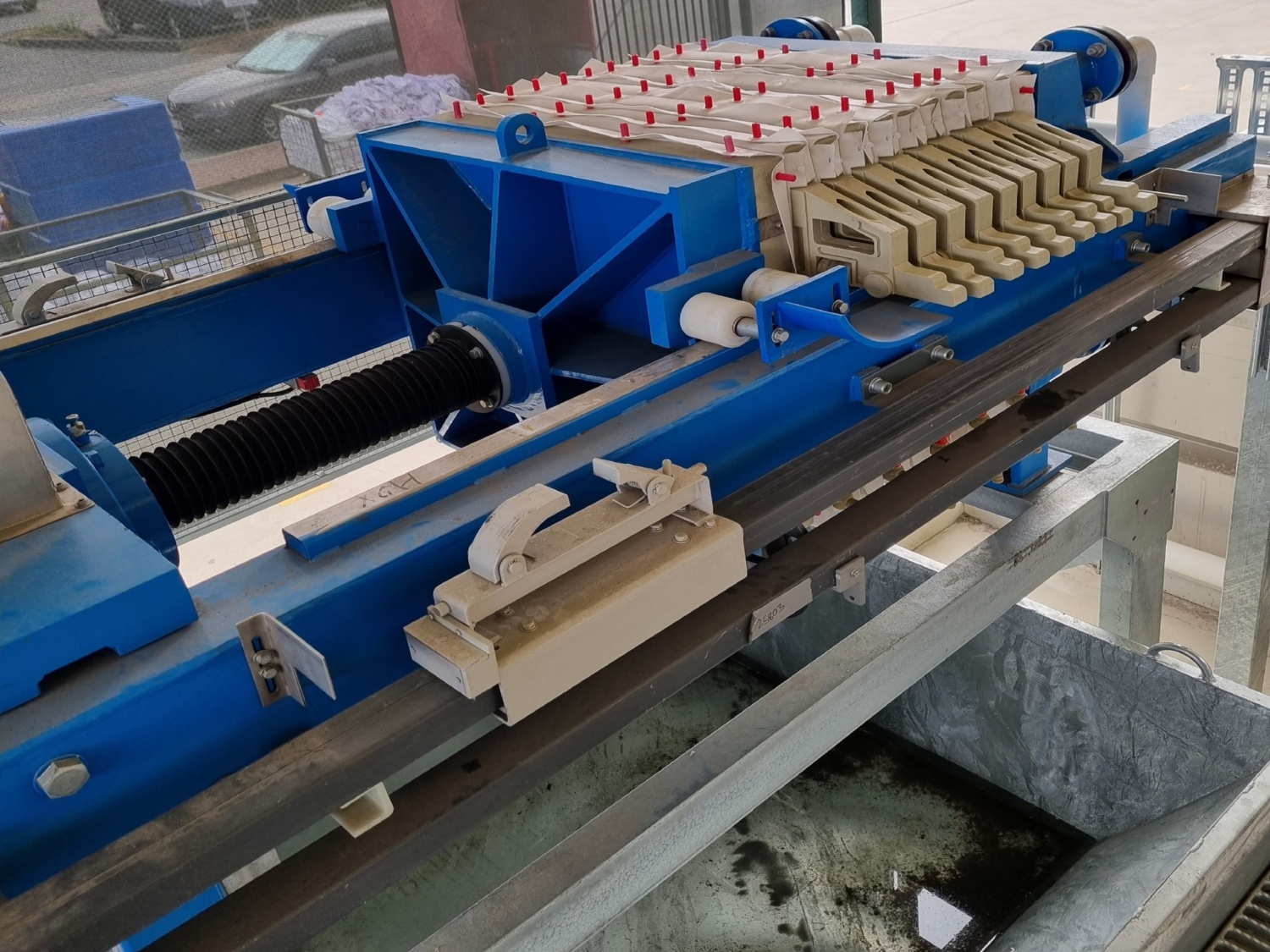
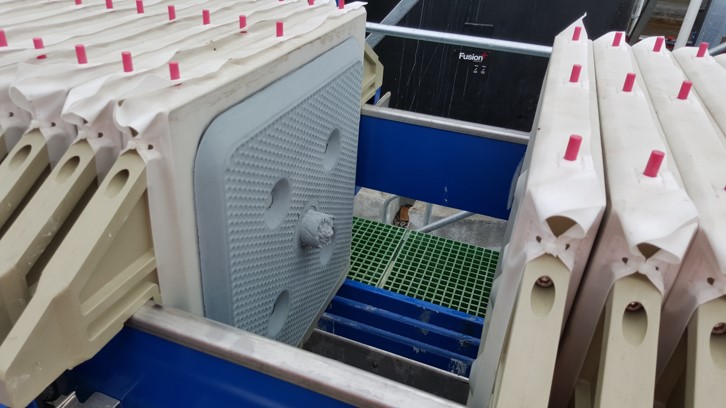
Membrane Plates
Membrane plates in a filter press are specialised plates equipped with flexible diaphragms that expand and contract to enhance dewatering efficiency by improved cake dryness and reduced cycle times. They are particularly beneficial for dewatering sludge that is highly compressible or difficult to filter.
Initially, the filter press operates conventionally, with sludge pumped into the chambers between the plates, allowing solids to accumulate on the filter cloths and form a cake. Once the initial filtration phase is complete, the membranes are inflated using air, water, or another fluid, mechanically compressing the cake to remove additional moisture. These features make them ideal for industries requiring highly efficient dewatering, such as mining and infrastructure.
CakeMax Filter Press Capacities
Hydroflux CakeMax filter presses are available in various plate sizes, configurations, and automation levels. The capacity of a CakeMax filter press is determined by the volume of dewatered cake produced per batch, which depends on plate size, the number of plates, cake dryness, and filtration cycle duration.
The table below provides indicative cake volume capacities for different plate sizes. The daily capacity varies based on the dewatering cycle time, which is influenced by the specific application. Semi-automated models typically operate between 1 to 4 cycles per day, while fully automated versions can exceed 24 cycles per day.
Sizing Table
Plate Size | Cake Volume Litres – Chamber Plates | Cake Volume Litres – Membrane Plates |
470mm square | 25-150 | – |
500mm square | 40-170 | – |
630mm square | 100-410 | 110-460 |
800mm square | 350-850 | 500-1200 |
1000mm square | 760-1550 | 750-1850 |
1200mm square | 1020-2400 | 1600-3700 |
1300mm square | 1300-3400 | 1900-4900 |
1500mm square | 1800-4700 | 2500-8500 |
Filter Press FAQs
The dryness of the filter cake from a filter press is influenced by factors such as sludge composition, filtration pressure, plate design, and the use of membrane squeezing. For primary sludge from clarification in infrastructure or manufacturing processes, standard chamber filter presses typically achieve 30–50% dry solids. However, membrane filter presses can attain 60% or higher by applying additional mechanical compression after the initial filtration phase, significantly enhancing dewatering efficiency.
The lifespan of filter cloths in a filter press depends on several factors, including sludge composition, operating pressure, cleaning frequency, and overall maintenance practices. Under normal operating conditions, filter cloths can last several months to a few years, (years is more common) but their longevity varies depending on how abrasive or sticky the sludge is and how frequently the press is used.
Regular maintenance and proper cleaning can extend the life of filter cloths. Washing the cloths after each cycle prevents clogging and maintains permeability, ensuring efficient filtration. Over time, cloths may degrade due to chemical exposure, high pressures, or wear from repeated use. Signs that a filter cloth needs replacement include reduced filtration efficiency, excessive cake sticking, increased cycle times, or visible damage such as tears or thinning fabric. Using high-quality filter cloths and following proper care procedures can significantly improve performance and reduce operational costs.
In certain applications such as mineral processing, infrastructure and some manufacturing processes, a filter press offers several key advantages over alternative dewatering technologies, such as centrifuges, belt presses, and screw presses. One of the most significant benefits is its ability to produce a drier filter cake, which leads to lower sludge disposal costs compared to other technologies. However, the filter press operates in a batch process, meaning it is not suitable for handling large volumes of slurry continuously, where other technologies may perform better. Additionally, filter presses may not be as effective when dealing with greasy or highly viscous sludge, which can impact filtration efficiency.
The time required to empty a semi-automated filter press varies depending on its size, the number of plates, and the characteristics of the filter cake. On average, a small to medium-sized press (10-80 plates) takes 5-30 minutes, while larger presses with more than 80 plates may take 30-60 minutes. Semi-automated systems typically include a plate shifter to assist with opening and closing the plates, but the operator is still required to monitor and manually intervene if cakes do not discharge properly.
Several factors influence the emptying time, including the cake’s texture and adhesion to the filter cloth. If the cake is dry and releases easily, the process is quicker, but sticky or fibrous cakes may require additional scraping or agitation. The efficiency of the plate shifter mechanism and the operator’s experience also impact the overall time. For operations that require frequent cycles, upgrading to a fully automated filter press is recommended.
Why Choose Hydroflux to Design and Construct Your Dewatering System?
At Hydroflux, we are committed to delivering high quality filter presses with exceptional build quality. We ensure that every system is built to last and operates with maximum efficiency, ensuring long-term performance and reliability.
With years of experience in the wastewater treatment industry, Hydroflux has the technical expertise to design and construct dewatering plants utilising filter presses technology and tailored to meet the specific needs of your facility. Our team has completed numerous installations, providing solutions that exceed client expectations in both performance and cost-effectiveness across many industrial sectors.
Choosing Hydroflux means selecting a trusted partner that combines high-quality systems, specialised equipment, and deep industry expertise to deliver outstanding sludge dewatering and wastewater treatment solutions.
Contact us for a discussion on dewatering options for your site.
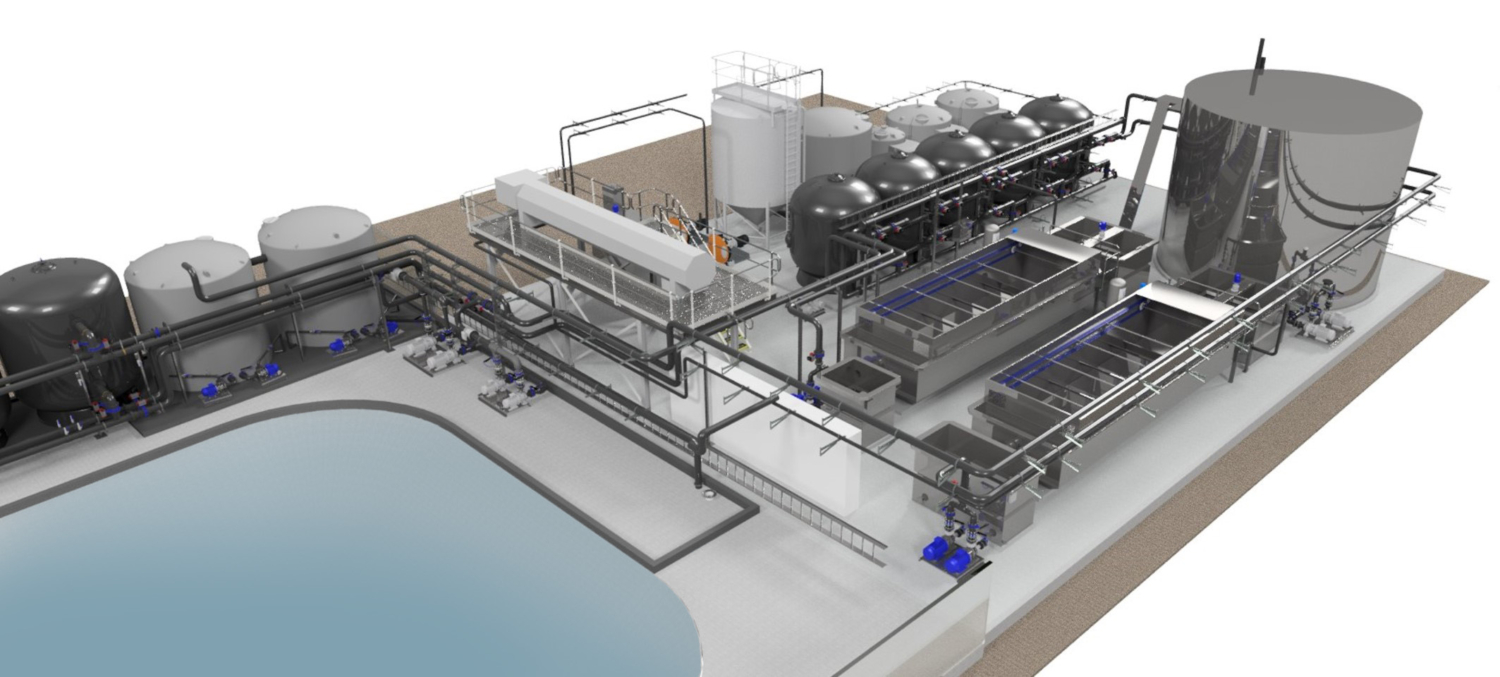
Sustainable Solutions
As Australia’s first certified carbon-neutral water and wastewater chemical supply and service business, we focus on sustainability. Developing and delivering sustainable solutions for treatment plant operation and maintenance is at the core of what we do. Our equipment is the most sustainable in the Australian and New Zealand markets and is also carbon-neutral. Click here to find out what this means for you
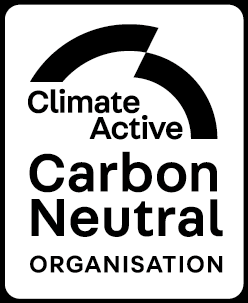